Aluminum is the main material in manufacturing conductors of wire and cables, and its function is to transmit current and electric power. Due to the different application environments, cables must bear their own weight and external loads such as wind, snow, ice, etc., and will also be eroded by chemical substances contained in the surrounding air. Aluminum conductors must have good electrical properties, sufficient mechanical strength and corrosion resistance.
What causes corrosion on aluminum?
Due to long-term exposure to the air, the aluminum in the cable has a working temperature as high as 70-80°C, which is higher than the ambient temperature, and is easily corroded under the action of water vapor, chemical gas, and salts in the air. The level of corrosion is closely related to the material composition and manufacturing process of the wire. The corrosion forms of wires include notch corrosion, electrochemical corrosion, pitting corrosion, and electrochemical corrosion is the main type of corrosion.
- Notch corrosion. There is a gap between the adjacent aluminum wires in the same layer and between the inner and outer aluminum wires to form a notch. When the oxygen in the gap is exhausted, an oxygen concentration difference will be formed inside and outside the gap, forming a gap with the outer wire as the cathode and the inner wire as the anode. Oxygen concentration difference battery accelerates corrosion. When the oxide film of the outer Al wire is destroyed, notch corrosion will occur between the wires of the same layer and different wires. Dust in industrial pollution areas not only contains a large amount of SO4 2-, NH4 + and Cl- ions, but also easily absorbs SO2 and water vapor in the atmosphere, thus forming a corrosive electrolyte and forming a local micro-battery on the ACSR wire, causing the internal and external aluminum wires to be damaged. Pinhole corrosion occurs. In addition, notch corrosion also occurs between aluminum cores.
- Pitting corrosion. When the passivation film on the surface of the aluminum wire is destroyed, an Al/Al2O3 "activation-passivation" primary cell of large cathode and small anode will be formed on the surface of the aluminum wire. Due to the large potential difference in the corrosion cell, the tiny anode area generates a large corrosion current, which accelerates the corrosion of the aluminum wire and causes pitting on the surface of the aluminum wire. Once formed, pits continue to grow through a self-sustaining process. The outer aluminum wire is susceptible to pitting corrosion, while the inner aluminum wire is less pitted due to the protection of the outer aluminum wire.
- Condensed into a water film, atmospheric O2, CO2 and other gases such as H2S, NH3, SO2, NO2, Cl2, HCl, etc. and salts are dissolved in the water film to form a thin layer of electrolyte. The thin layer of electrolyte reacts with the metal oxide film and produces pitting corrosion. In the aluminum core contact layer inside the wire, due to the difference in the potential of the metal electrodes, contact corrosion will also occur. After the aluminum strands are corroded, white powder will be produced on the surface and covered with pockmarks, and white powder will also be produced on the contact layer of the aluminum core. At the same time, the wire will become brittle and the tensile strength will be significantly reduced. In severe cases, it will cause broken strands and wires, which greatly shortens the service life of the wires.
- Intergranular corrosion. Due to the difference in the composition and atomic arrangement phase composition of aluminum at the grain boundary and within the grain, there are differences in the corrosion rate. Intergranular corrosion occurs when the corrosion rate at the grain boundaries exceeds the rate of corrosion within the grains. Solute atoms segregated at grain boundaries can accelerate localized corrosion. A certain element in the matrix is consumed due to precipitation at the grain boundary, which reduces the corrosion resistance of the matrix. It is more common in the corrosion process of stainless steel. Due to the segregation of grain boundary impurities and misalignment of grain boundary atoms, aluminum is prone to intergranular corrosion, and aluminum will also preferentially form corrosion pits at the intergranular position.
Aluminum Corrosion Hazards in Cables
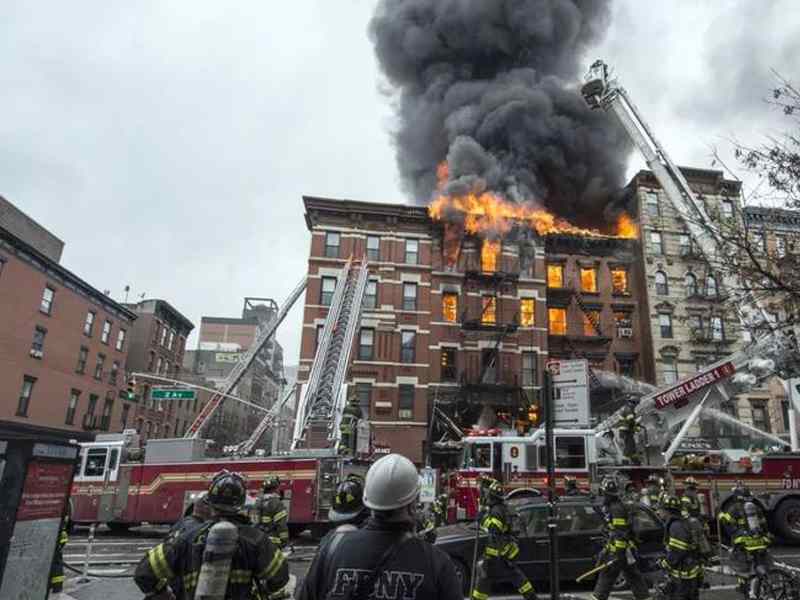
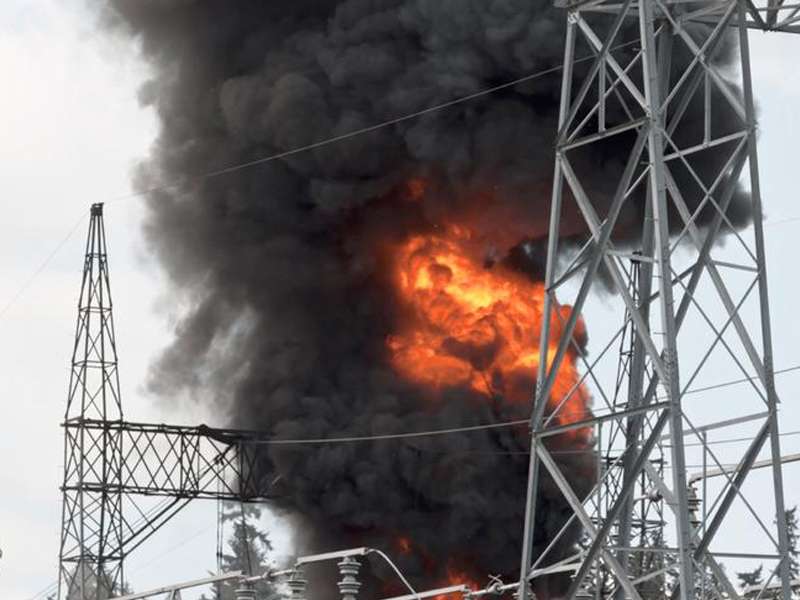
Aluminum conductor is the main conductor material of high-voltage transmission lines, and its safe and reliable operation is very important to ensure the safe transmission of electricity. However, due to the erosion of moisture, chemical gases and salt media in the atmosphere, it is prone to corrosion, blackened and brittle on surface, and reduced strength. In severe cases, strands and wires may even break, causing safety accidents. and affecting power transmission safety.
Power outage accidents happen all over the world from time to time, which raises power safety to the level of national security. Through research on the causes of broken strands of transmission lines at home and abroad, it is generally believed that the corrosion of the line itself is a potential killer that leads to broken strands. The American Electric Power Research Institute (EPRI) and the Canadian Power Tech Lab have listed corrosion management issues such as transmission network corrosion assessment, control and protection as important research topics in transmission network management.
How to Protect Aluminum Cables From Corrosion
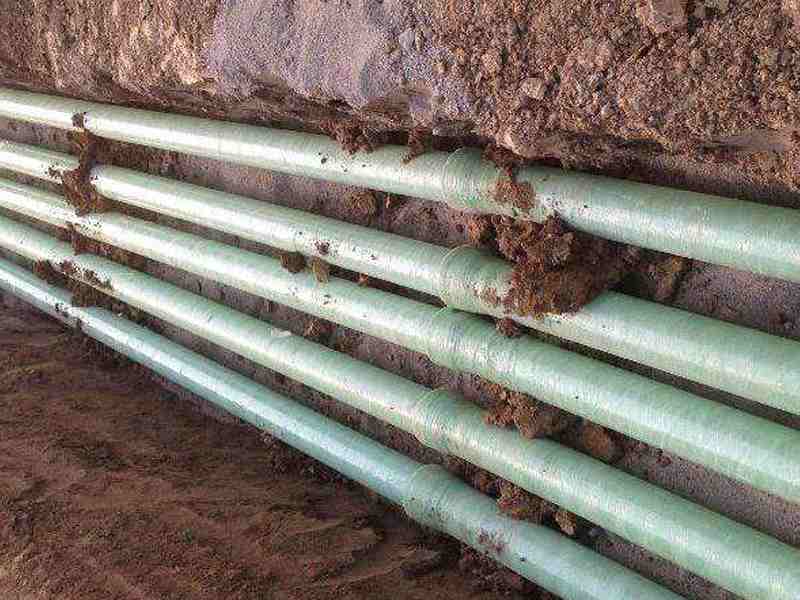
At present, the anti-corrosion measures for aluminum wires mainly include the following methods: coating the aluminum core with anti-corrosion paint, adopting hot-dip galvanizing for surface anti-corrosion treatment of the aluminum core, and manufacturing anti-corrosion aluminum wires. In order to improve the corrosion resistance of the aluminum wire, the aluminum core is usually coated with organic anti-corrosion grease to prevent the corrosion of the aluminum core by rain and corrosive gases, so as to prolong the life of the aluminum core.
Because anti-corrosion grease will increase the weight of the wire, long-term use will cause the wire to age and fail, so people began to use the method of direct galvanizing on the surface of the aluminum core for anti-corrosion. In order to improve the corrosion resistance of the galvanized layer, tin is added during the galvanized process. Because the galvanized layer and the wire are easy to form a galvanic couple corrosion, people have manufactured an aluminum-clad steel-reinforced aluminum stranded wire that makes the contact between the load-bearing and the conductive part of the wire the same metal, which prolongs the life 1 times longer than the wire. Later, in order to improve the overall performance of the wire, rare earth aluminum stranded wire and steel core rare earth aluminum stranded wire were manufactured, which extended the life of the wire by more than 3-4 times. This type of wire has good anti-corrosion performance and is suitable for high-voltage, ultra-high-voltage and general power transmission and distribution lines in coastal saltwater lakes, saline sandy soil areas and industrial areas.
Conclusion
The rapid development of the modern economy puts forward higher requirements for the power industry, and also promotes the continuous progress of power transmission technology. As a transmission carrier, aluminum wire plays an extremely important role in transmission lines. In order to ensure the safety and reliability of power transmission, it is becoming more and more important to protect the aluminum in cables from corrosion.