Mineral insulated cable is a special cable composed of copper core, copper sheath, and magnesium oxide insulation. In order to ensure the construction and installation quality of this kind of cable, it is necessary to fully understand the structure, performance, and characteristics of Mineral insulated cable; understand the type, specification, and type of cable. and where applicable. It is also necessary to master the laying, installation methods, methods, and skills of Mineral insulated cables, and understand the precautions in laying construction, such as the bending radius of cables, the arrangement of laying, how to enter and exit distribution boxes, and cabinets, how to pay attention to eliminating eddy currents, etc. . It is also necessary to understand the special tools required for the installation and construction of Mineral insulated cables and be proficient in their use.
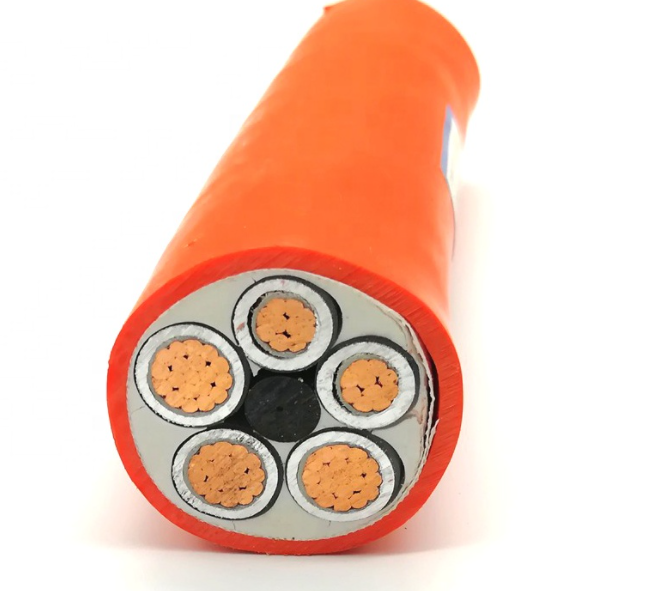
Before installing:
Familiarize yourself with the construction drawings and site conditions before installation, and plan and formulate a construction plan. During the laying process of the cable, or after the laying and installation, it is strictly forbidden to drag or collide with the electric welding faucet wire on the cable, because the electrified electric welding faucet wire will contact the copper sheath of the Mineral insulated cable (equivalent to the ground wire) Butt welding sparks are generated, so that the copper sheath is melted, resulting in holes in the copper sheath of the cable, causing the moisture in the air to be absorbed by the magnesium oxide insulation, and the insulation resistance value of the cable is reduced. Sometimes the faulty segment that produces the hole cannot be found.
When installing:
Special construction tools should be used during the construction of BTTZ cables. The tools should include but are not limited to stripper presser, compression, straightener, and bender for end caps.
During the laying and installation process, the insulation of the cables should be tested frequently, and problems should be dealt with in time. The insulation resistance value of the cable should be measured several times before and after the cable is laid and the terminals and intermediate joints are made, and the comparison before and after is carried out to ensure that the quality of the cables in each installation step is intact. At the same time, no matter whether the cable is cut off or suspended for construction, or needs to be placed for a period of time before construction, the cable must be sealed in time to prevent the magnesium oxide insulating layer from getting damp.
Post-installation detection:
An insulation test is carried out immediately after the cable terminations and intermediate joints are installed, and again after 24 hours. If there is no dampness when the cable is installed and installed at the terminal or the intermediate head, and the sheath is not damaged, the insulation resistance value of the cable should be converted to a length of 1000m and not less than 1000 megohms at room temperature. In the actual test, the pointer of the megohmmeter should point to 'C', which means that the performance of the cable line is good. If the insulation resistance value is found to drop in the second measurement, the fault point should be found. Generally speaking, the fault point is at the terminal or the intermediate joint. When looking for it, the torch flame can be used at the lower part of the terminal head, and the two parts of the intermediate joint can be found. After heating for a few seconds, the insulation resistance of the cable drops sharply, indicating that there is a problem with the terminal or the intermediate head. At this time, the terminal or intermediate head should be removed, and the cable should be heated with a torch flame until insulation. qualified. If the insulation resistance value does not change, other terminals or intermediate heads on the line should be checked until the fault is found, and repaired according to the above method.
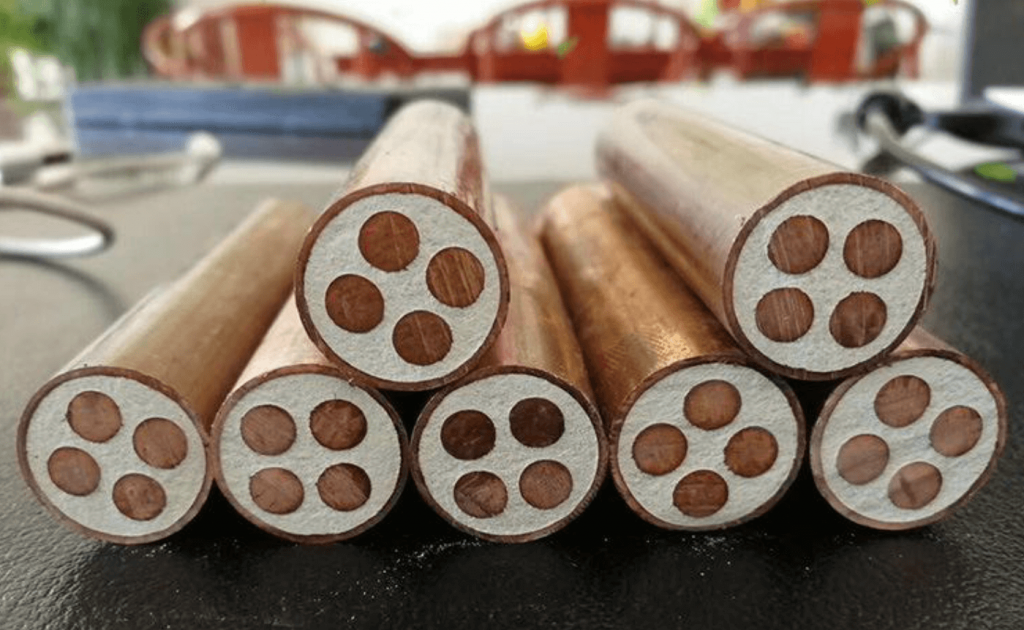
Installation and Maintenance Precautions:
1. There are two types of cable laying: vertical laying and horizontal laying. When laying in the same direction, it should be based on the position of the fork of the cable.
Place the cables one by one from near to far to avoid cables crossing and affecting the appearance.
2. When laying, pay great attention to the pulling of the cable, and do not continuously drag and rub the cable on the ground, rough walls, or hard objects.
3. It is absolutely forbidden to drag the cable on hard and sharp objects and be hit by sharp objects.
4. It is strictly forbidden for the live electric welding faucet and its circuit to directly or indirectly contact or collide with the cable.
5. Ensure that the copper sheath of the cable is well grounded when wiring.
6. The copper sheath of the Mineral insulated cable can be used as a ground wire, but it must be grounded, and one end is grounded.
7. During on-site construction, the transportation of Mineral insulated cables can be carried out manually. If conditions permit and the handling tools are available, it is also possible to use mechanical handling, but the protection of the cables should be done during handling to avoid damage to the cables.