To avoid and reduce the occurrence of low-voltage cable faults, minimize losses to people, and ensure normal power use, relevant departments must strengthen the daily maintenance of cable lines, improve their safety operation level, and eliminate all external factors that may affect line safety.
What is Low-Voltage Cables ?
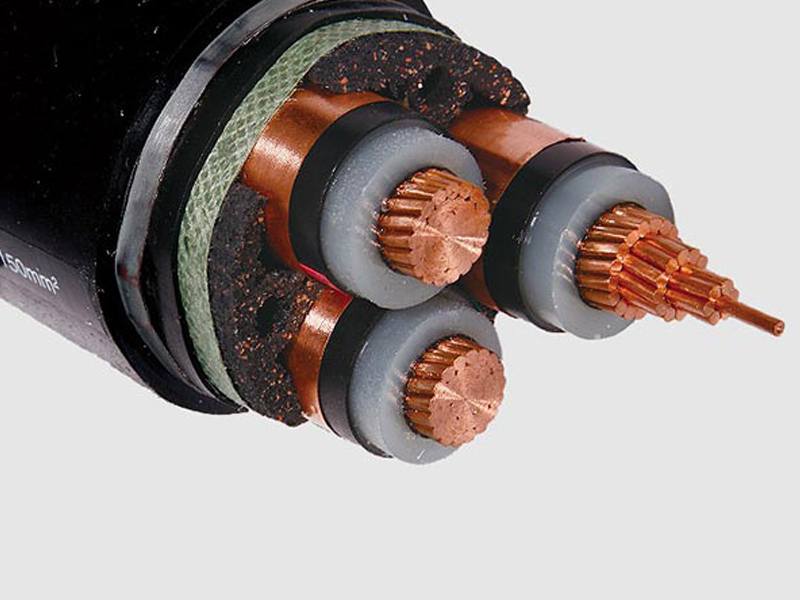
The electric power industry uses several basic types of low-voltage cables, which are divided into two categories:
① according to special-purpose cables: flame-retardant cables, fire-resistant cables, halogen-free low-smoke cables, fire-resistant cables, etc.
② divided according to cable core material: cross-linked polyethylene insulated polyvinyl chloride sheathed (copper core) power cables, polyvinyl chloride insulated polyvinyl chloride sheathed (copper core) power cables.
Common low-voltage cables have single-core and multi-core cables with various combinations, and the commonly used ones are 3, 4, and 5 cores, among which 4 and 5 cores are of the same diameter or unequal diameter, corresponding to 3+1 and 4+1 or 3+2, respectively. The N-line and PE line of unequal diameter cables are in accordance with national standards, such as 4×185+1×95 or 3×185+2×95. Its specifications are divided into: 1.5, 2.5, 4, 6, 10, 16, 25, 35, 50, 70, 95, 120, 150, 185, 240, 300, etc. according to the wire diameter model.
Operating Standards for Low-Voltage Cable Lines
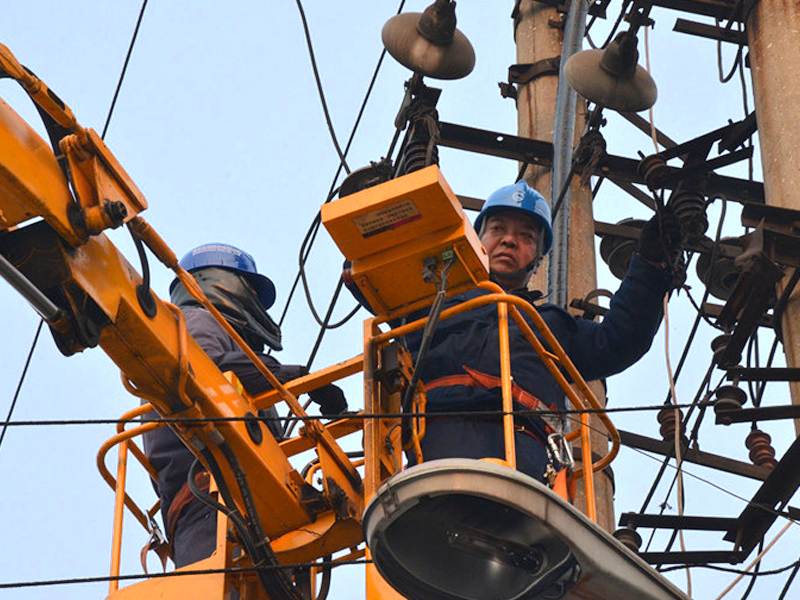
To overcome the concealment of cable lines, the incomplete operating data of individual operating units, and the limitations of testing equipment, it is necessary to strengthen the search for low-voltage cable faults and maintenance of low-voltage cable lines. Cable faults can be classified into two types according to their nature: series and parallel faults. Therefore, judging the insulation condition of low-voltage cables has become an important link for the electric power industry to judge the cable operating conditions and prevent losses of power facilities.
- Requirements for Cable Operating Voltage
The operating voltage of the cable should not exceed 1.15 times its rated voltage. For example, in a 6kV system, when a single-phase ground fault occurs, the faulty line will not automatically trip out of operation, but it can cause the system phase voltage to increase by 1 to 1.73 times. At this time, the operation of the cable line or segment should not exceed 2 hours to prevent insulation breakdown. Backup or infrequently used cables should also be charged on the power grid to prevent moisture. - Requirements for Cable Temperature
The cable temperature, especially the core temperature, must not exceed the allowable temperature of the corresponding cable material. The core temperature is difficult to measure, but the outer skin temperature is easy to measure, and the difference between the outer skin temperature and the core temperature is generally about 15 to 20℃. The cable temperature rise will reduce the insulation performance of the cable and cause the insulation material to age. Therefore, during the operation of the cable, it should not exceed its allowable temperature rise. If the cable temperature exceeds the allowable temperature rise, the load should be limited, and the temperature should be reduced by controlling the current. - Requirements for Cable Line Impedance
The capacitive component of the cable line impedance is relatively large, so after the cable line with all cables laid is tripped, no test power is allowed. The reasons are: ① because cable line faults are generally permanent faults, test power will only expand the scope of the accident and increase losses; ② if the unloaded cable line is powered off, if test power is immediately applied, it will cause insulation weak links of the line due to operation overvoltage, leading to accidents. - Cable Lines Cannot Overload
Cable lines should not be overloaded, as overloading will cause heating, and cables with a long-term current lower than the maximum long-term operating current are allowed to overload for a short time, but should meet specific requirements. - Main Manifestations of Low-Voltage Cable Faults
The main manifestations of low-voltage cable faults are open circuit, short circuit, and break circuit. Low-voltage cables also have the following characteristics in practical use: the randomness of laying is relatively large, the path is not very clear; during laying, it is not deeply buried like high-voltage cables after sand filling and brick laying, but rather shallowly buried, making it susceptible to external damage and faults; secondly, the cable is generally short, ranging from tens of meters to several hundred meters, unlike high-voltage cables that are often several hundred meters to several kilometers, which brings many inconveniences for the inspection and maintenance of low-voltage cables; thirdly, most low-voltage cables have obvious burning and damage at the fault points; fourth, the load carried by low-voltage cables changes greatly and is often unbalanced between phases, which is easy to cause heating and many faults.
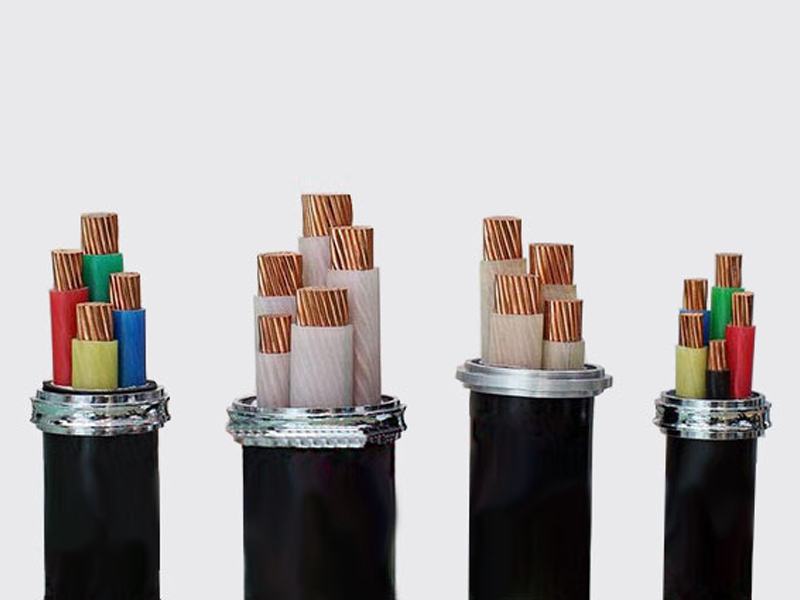
Methods of Low-Voltage Line Maintenance
- Establishing a Regular Inspection System for Low-Voltage Cable Lines
Frequent inspection of cable lines is an effective measure to prevent external damage, avoid terminal head and junction box defects that cause faults.
Establishing an efficient, scientific, and comprehensive system for regularly inspecting low-voltage cable lines, fully mobilizing the enthusiasm of workers, and letting everyone participate in the inspection of power cables. For the hidden dangers and problems found, countermeasures should be taken in a timely manner to eliminate them. - Strengthening Corrosion Control and Terminal Head Maintenance of Low-Voltage Cables
Cable lines are prone to corrosion, so in the maintenance of low-voltage cable lines, corrosion control should be strengthened. When a solution corroding the cable lead sheath is found in the soil, appropriate improvement measures and protection methods should be taken, and the discharge of wastewater from nearby factories should be immediately investigated. If the local soil on the cable line contains chemicals that damage the cable lead sheath, the cable should be coated with asphalt, and the cable should be placed in a pipe and padded and covered with neutral soil. Also, to prevent chemical corrosion of the cable, the soil on the cable line must be chemically analyzed correctly, and the chemical analysis data of the corrosive substances and soil must be recorded in a special file.
In terms of terminal head maintenance, when maintaining low-voltage cable lines, the maintenance of the terminal head should be strengthened. In daily maintenance, check whether the terminal head lead-out wire is in good contact and whether the grounding meets the requirements. Always check the line name and phase color, check the support and cable armor, and paint to prevent corrosion. Clean the terminal head, check for corona discharge marks and oil leakage. And find solutions and requirements for all problems. - Improving the Maintenance Methods of Low-Voltage Cable Lines
At present, the maintenance methods for low-voltage cable lines in use are relatively traditional and the maintenance level is average. In order to better maintain low-voltage cable lines, we should actively use new varieties, promote new technologies, and improve the operation level of cable lines. For example, cross-linked cables are used for high voltage, and polyvinyl chloride cables are used for low voltage. Indoor and outdoor terminal heads and junction boxes are promoted to use heat-shrinkable heads, which can effectively improve the operation level, reliability, and safety of power supply.
Conclusion
Although there have been many changes in the operation of cables, the fundamental work of cable operation must still be done well. However, due to changes in operating conditions, inspection items that were not key before have become key inspection items, and operating content that was ignored because of long-term absence of problems has become very important. Therefore, as long as we rely on scientific management, apply standardized standards, and quantify assessed indicators, we can effectively avoid many faults of electric power cables by doing each specific job well.