Mineral insulated cables are essential fireproof cables for power transmission in modern construction projects. According to statistics, most high-rise buildings in the market need to use mineral insulated cabless, and the market application is very mature.
What is mineral insulated cables ?
Mineral insulated cables is a kind of cable with annealed copper as conductor, dense magnesium oxide as insulation and annealed copper tube as sheath. Mineral Insulated Cable is referred to as MI cable. When used as wiring, it is commonly called magnesium oxide cable or fireproof cable in China. It is a copper core copper sheath cable with mineral material magnesium oxide powder as insulation, and the mineral insulated cables is composed of two inorganic materials: copper conductor, magnesium oxide and copper sheath.
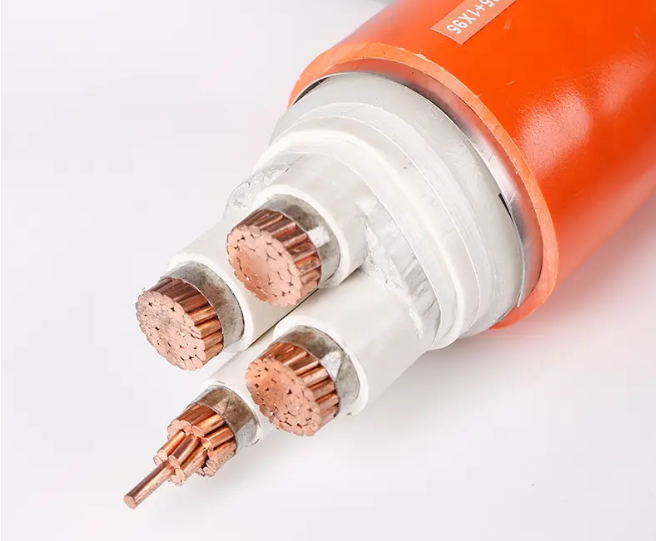
Mineral insulated cables (MI cable) advantages:
1. High operating temperature: Mineral insulated cables can withstand continuous operating temperatures up to 250°C.
2. Fire resistance: copper and magnesium oxide, the two materials used in mineral insulated cables, are inorganic substances. This kind of cable will not burn or support combustion, and can continue to operate under conditions close to the flame;
3. Explosion-proof: The highly compacted insulating material in the mineral insulated cable can prevent the passage of steam, gas and flame between the equipment parts connected to the cable;
4. Long service life: The inorganic materials used in mineral insulated cables can ensure the stability, long service life and fire resistance of the cables;
5. Waterproof: If the mineral insulated cable is completely immersed in water, with its seamless metal sheath, the mineral insulated cable can continue to operate;
6. Small outer diameter: The diameter of the mineral insulated cable is smaller than other cables with the same rated current;
7. High mechanical strength: The mineral insulated cable is sturdy and durable, and can withstand severe mechanical damage without damaging its electrical properties;
8. Large current carrying capacity: For cables with the same cross section, mineral insulated cables transmit higher current than other types of cables, and at the same time, mineral insulated cables can withstand considerable overload;
9. High corrosion resistance: The copper sheath of the mineral insulated cable has high corrosion resistance, and for most devices, it does not require additional protective measures. Where the copper sheath of the cable is susceptible to chemical corrosion or industrial pollution, mineral insulated cables should be protected by a plastic outer sheath;
10. High short-circuit fault rating: At the same temperature, the short-circuit fault rating of mineral insulated cables is significantly higher than other types of cables;
11. Good grounding: For mineral insulated cabless, independent grounding conductors are not required, because the copper sheath used in this cable has played the role of grounding conductors, which can provide excellent low grounding resistance.
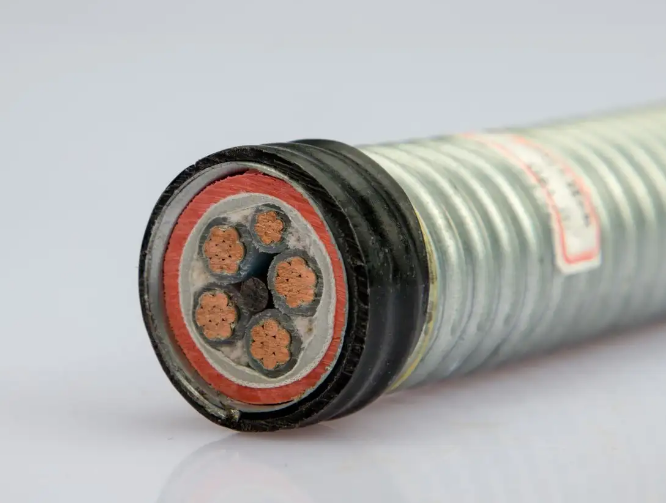
About the price of mineral insulated cables
Mineral insulated cabless can be reduced by 1 to 2 gauges and save a ground core:
Most people think that mineral insulated cabless are expensive and do not use them, but they are not. Through the continuous efforts of manufacturers and material suppliers in recent years, the price of mineral insulated cabless is constantly moving closer to the price of ordinary cables. Mineral insulated cabless with a cross-section of more than 25 mm2 are single-core, so the current carrying capacity of the cable is higher than that of ordinary cables. The current carrying capacity of the mineral insulated cables should be large, and this conclusion is also drawn from the experiment of simulating the characteristics of the physical cable. At the same time, the copper sheath of the mineral insulated cables can be directly used for the ground wire, so that one cable core can be reduced when the mineral insulated cables is selected.

Mineral insulated cables applications
Due to the excellent performance of the mineral insulated cables, it is suitable for fire protection and the following lines with a rated voltage of 1000V and below:
General lighting, emergency lighting circuit, emergency broadcasting circuit, emergency elevator and lifting equipment circuit, fire alarm control circuit, computer room control circuit, fire electrical circuit, generator room transmission circuit, power supply circuit that cannot be cut off, dual power supply control circuit, public Place lighting lines, trunk/sub-main power distribution system lines, scenic spots and historical sites lighting lines, high temperature environment power and control lines, oil pump lines, lines in potentially dangerous and explosive areas.
Knowing the characteristics of mineral insulated cabless, what are the construction points of mineral insulated cabless?
1. The joint is susceptible to moisture. The insulating layer of the cable is composed of the mineral magnesium oxide. During the construction of the cable head, when the conductor is exposed after the cable end is stripped, it is easy to chemically react with the moisture in the air to generate conductive magnesium hydroxide. The insulation resistance of the cable is generally above 100MΩ, but if the production of the cable head is completed within 1h, the insulation resistance can be reduced to below 10MΩ, or even below 0.5MΩ. In this way, the use of cables in projects will inevitably bring electrical hazards.
2. The cable loop should be marked with the number, and the loop number and phase sequence should be marked at the end point, start point, and intermediate joint of each loop. In order to avoid errors caused by too many phase sequence loops.
3. Mineral insulated cables are mostly single-core cables to form circuits in engineering, so eddy currents are easily generated in the cable fixing hardware. If the eddy current is too large, it will not only cause a lot of loss, but also accelerate the aging speed of the fixed hardware of the cable. Therefore, in the actual construction, the eddy current should be avoided or minimized as much as possible. Therefore, in the field, the cable fixing fittings usually need anti-eddy current measures, and at the same time, a reasonable cable phase sequence is used to minimize the eddy current.
To sum up, the quality of the power cable directly affects the operation safety of the line. Once the line cannot operate safely and stably, the life and economic losses caused by its failure are unpredictable. Therefore, our cable fundamentally prevents the cable In the event of a fault, try to reduce cable accidents as much as possible, start from the subtle, and strive to achieve the goal of safe and reliability.